The Q & T Process
The quenching
& tempering process as per Thermex® makes use of the heat energy of the rolled bar after the finishing stand
of the rolling mill. Normally, this energy is wasted as the rolled bars at 950-1000 0C are allowed to cool to ambient
temperature on the cooling bed. The Thermex® process is a sophisticated and precise technology that has been developed
after years of trials and tests.
The Thermex®
System is installed between the last mill stand and the cooling bed. (See Fig. 1)
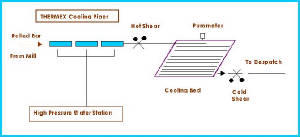
|
Fig. 1: Thermex® System in a rolling mill. |
The bar
as it leaves the last stand is guided through specially designed proprietary Thermex® Pipes wherein the surface
temperature of 950-1000 0C is brought down drastically in a relatively short period of time - approximately 1 sec
- on account of the intense and uniform cooling. The temperature of the core is largely unaffected. The name THERMEX is derived
from thermal exchange and this exchange is the
key to the process.
The drastic
and pre-determined cooling of the bar periphery transforms the peripheral structure to martensite and would necessarily need
to be annealed to render the bar useful. This annealing is achieved through the heat available at the core. The peripheral
and core temperatures finally equalise at around 600 0C and the resultant bar structure is of tempered martensite
at the periphery and of fine-grained ferrite-pearlite at the core. Generally speaking, the resultant soft core forms about
70 – 80 % of the area (depending upon the desired minimum yield strength) and the rest is the hardened periphery. The
product exhibits high yield point, surface hardness, toughness, ductility and weldability.
The thermal
exchange in the quenching and tempering process is depicted in diagrams Fig 2a and 2b.
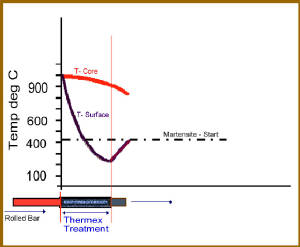
|
Fig. 2a |
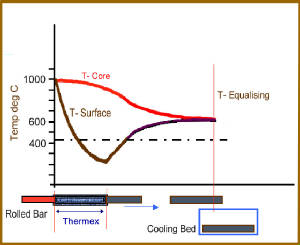
|
Fig. 2b |
The specially designed Thermex® pipe assembly
consists of chambers, nozzles and guide inserts, venturi guide etc. The pipe is designed in such a way that high pressure
water jets flows in the rolling direction, creates uniform water pressure all around the surface of the bar, and keeps the bar floated in guide inserts when it passes
through the Thermex® pipe. The
result is the uniform intensive cooling all around the surface of the bar.
The final
product cross-section is shown alongside in Fig.3.
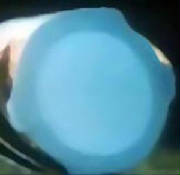
|
Fig.3 Note the uniform hardened periphery and soft core. |
|